How to Optimize the SKUs in Your Warehouse
Efficient warehouse management is crucial for businesses looking to streamline operations and meet customer demands promptly. One key factor that significantly impacts warehouse efficiency is the number of Stock Keeping Units (SKUs) it houses. Determining the ideal number of SKUs for your warehouse environment is a crucial decision that requires careful consideration.
In this blog post, we will explore important questions warehouse managers should ask themselves and the essential SKU data required for efficient warehouse design and management.
How Does Understanding Your SKUs Impact Warehouse Design?
It may seem like a headache, but determining the number of SKUs your warehouse can support is essential for efficient and effective operations. It allows you to balance offering a wide range of products and optimizing storage and handling capabilities. By accurately assessing your warehouse’s capacity, you can avoid overcrowding and disorganization, ensuring easy product access and streamlined workflows.
Understanding the ideal number of SKUs also helps inventory management, reducing carrying costs and minimizing the risk of stockouts or overstock situations. It also enables you to allocate appropriate storage solutions, such as racking systems or shelving units, based on the volume and characteristics of your SKUs. Crunching the numbers and discovering your capacity is the key to optimal space utilization, enhanced order fulfillment rates, and better customer service, all of which improve overall performance and profitability.
Gain the Insight to Refine Your Warehouse Storage Area
The variety and quantity of your SKUs directly influence the type of storage systems required to accommodate them efficiently. When you have more, you may need more versatile storage solutions that offer better flexibility and easy access, such as selective racking, carton flow, or carton shuttle systems. These allow for individual item picking and rapid retrieval.
If you have fewer SKUs but higher order volumes, you may benefit from bulk storage solutions like double deep, pushback, or drive-in pallet racking or mezzanine platforms that can handle larger quantities and optimize space use. Understanding your count and product characteristics enables you to select appropriate storage solutions that maximize storage density, accessibility, and overall operational efficiency.
What to Consider When Sorting Through Your SKUs
Discovering how many SKUs to house in your warehouse can be challenging. You have to deal with constantly shifting customer demand, seasonal variations, and sudden changes in consumer behavior. Nonetheless, understanding your practical limitations is vital to a successful warehouse operation.
Here are a few topics to explore when optimizing your warehouse:
Assessing Warehouse Capacity and Storage Space
Evaluate your warehouse’s capacity. Consider the physical size of your facility, available storage space, and shelving systems. Understanding the limitations of your warehouse infrastructure will help you make realistic decisions regarding the number of SKUs it can support effectively.
Customer Demand and Variety
Analyzing customer demand patterns and product variety can be a boon to your optimization efforts. You can get ahead of the curve and react fluidly to changing market conditions. Ask yourself the following questions:
- What are the most popular types of products?
- Are there specific seasonal or trend-based items that require additional storage space?
- How frequently do customers request different product variants?
Order Volume and Picking Efficiency
Consider the volume of orders your warehouse handles daily. High-order volume warehouses may benefit from more SKUs to ensure a wider product selection and faster order fulfillment. Warehouses with lower order volumes may need to balance SKU variety and operational efficiency more carefully to avoid excessive inventory and increased order-picking time.
Inventory Turnover Rate
Examining your inventory turnover rate provides valuable insights into the frequency at which SKUs move in and out of your warehouse. Faster-moving SKUs require more frequent restocking and should be given priority in terms of storage space and accessibility. By focusing on SKUs with high turnover rates, you can optimize your inventory management and reduce carrying costs.
Survey SKU Data for More Efficient Warehouse Design
To facilitate efficient warehouse design and management, the following SKU data is crucial:
SKU dimensions: Knowing each SKU’s dimensions enables proper space use and ensures accurate slotting and stacking.
Weight and load-bearing capacity: Understanding the weight of SKUs helps determine appropriate shelving and racking systems to ensure safety and prevent damage.
Velocity classification: Classifying SKUs based on their movement frequency (e.g., fast-moving, slow-moving, obsolete) allows for strategic placement and efficient picking processes.
Storage requirements: Some SKUs may have specific storage requirements, such as temperature control, fragile handling, or hazardous material considerations. Identifying such needs enables you to allocate appropriate storage areas and equipment.
Making successful changes to your warehouse operations is easier with a genuine collaborator. Polymatic shares your objectives, making suggestions to help improve your strategy. You remain in control throughout the project—we’re your allies in optimization.
SKU Rationalization
Warehouse managers should regularly conduct SKU rationalization exercises to identify and eliminate underperformance or redundancy. This process involves evaluating the profitability, demand, and contribution of each SKU to the overall business. Removing weak performers can free up valuable storage space and optimize inventory levels, increasing efficiency and cost savings.
Technology and Automation
Implementing technology and automation solutions significantly impacts the number of SKUs a warehouse can handle efficiently. Warehouse management systems (WMS), barcode scanning, and automated picking systems help streamline operations, reduce errors, and increase throughput. By leveraging these technologies, warehouse managers can effectively manage more SKUs while maintaining operational efficiency.
Warehouse Racking Configuration
The design and configuration of racking systems directly impacts the storage capacity, accessibility, and organization of SKUs. By using suitable systems like selective racking, double-deep racking, or pallet flow racking, warehouses can accommodate more while maintaining accessibility and minimizing handling time.
Well-planned racking systems also facilitate effective inventory management, allowing for proper SKU categorization and segregation based on size, demand, or other relevant factors. This promotes efficient order fulfillment, reduces picking errors, and improves warehouse productivity.
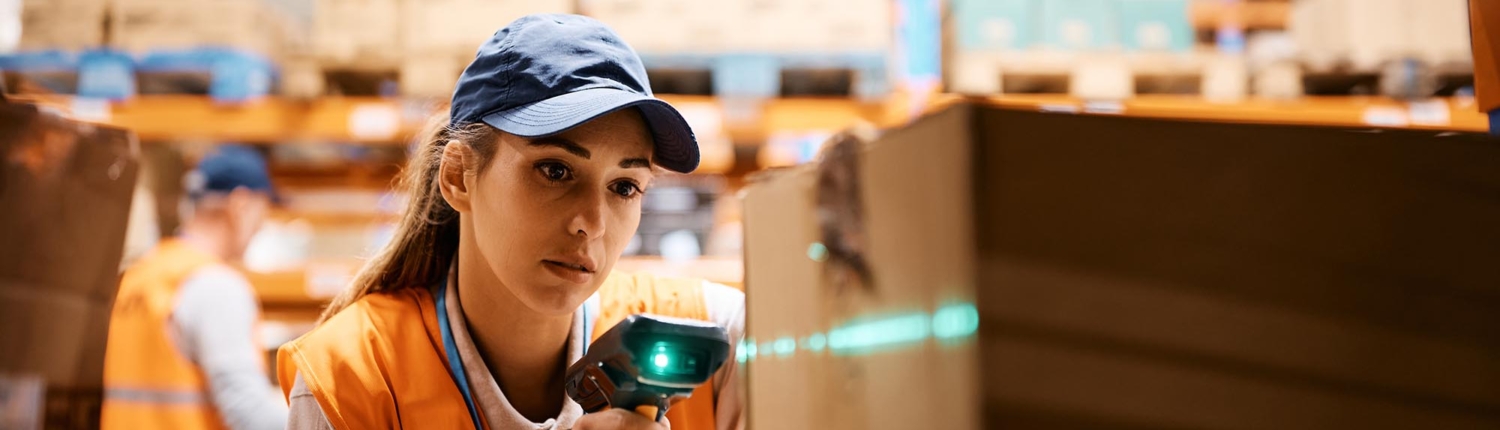
Collaboration with Suppliers and Retailers
Work closely with your suppliers to identify opportunities for consolidation, such as using similar packaging for multiple SKUs or implementing product variants that share common components. Collaborating with retailers can provide valuable insights into customer demand and preferences, allowing you to optimize your assortment based on market trends and consumer needs.
Flexibility and Scalability
Consider your business’s future growth and scalability when determining the number of SKUs in your warehouse. Anticipate changes in customer demand, market trends, and product offerings. Design your warehouse layout and storage systems with flexibility in mind, allowing for easy adaptation and expansion as your business evolves. This will prevent the need for frequent redesigns and minimize disruptions to your operations.
Continuous Monitoring and Analysis
Calculating your warehouse’s ideal number of SKUs is not a one-time exercise. It requires continuous monitoring, analysis, and adaptation. Regularly review key performance indicators (KPIs) such as order fulfillment rates, inventory turnover, and picking accuracy to identify areas for improvement. Analyze data and customer feedback to identify emerging trends and adjust your SKU assortment accordingly.
Make the Most of Your Warehouse Space Using Polymatic
You don’t need to tackle SKU optimization alone. We’re experts in the ever-changing world of logistics. We are well-versed in the kinds of machinery that make material handling a breeze, and we’re committed to helping facility managers reach their goals for improved warehousing operations. Our team can provide all the necessary tools to transform your operation totally.
Related Postings
Location
Get In Touch
Phone
(909) 644-7479
Services
About Us
At Polymatic, your design is our mission. We learn your short and long-term goals and provide stellar warehouse solutions that refine and reinforce your supply chain.